Services
We can offer you services ranging from design all the way to cleaning and packaging.
We are specialized in production of high precision Ø 0,35-65mm CNC turned & milled parts with a tolerance up to ±0,0025 mm.
Our experienced staff are capable of producing the most sophisticated parts from different types of stainless steel, aluminium (incl. 6082), plastic (PEEK, PPSU, POM), brass, copper and titanium. Optimum production batch size is 100 to 10,000 pieces.
Generally we have 6 distinct work steps:
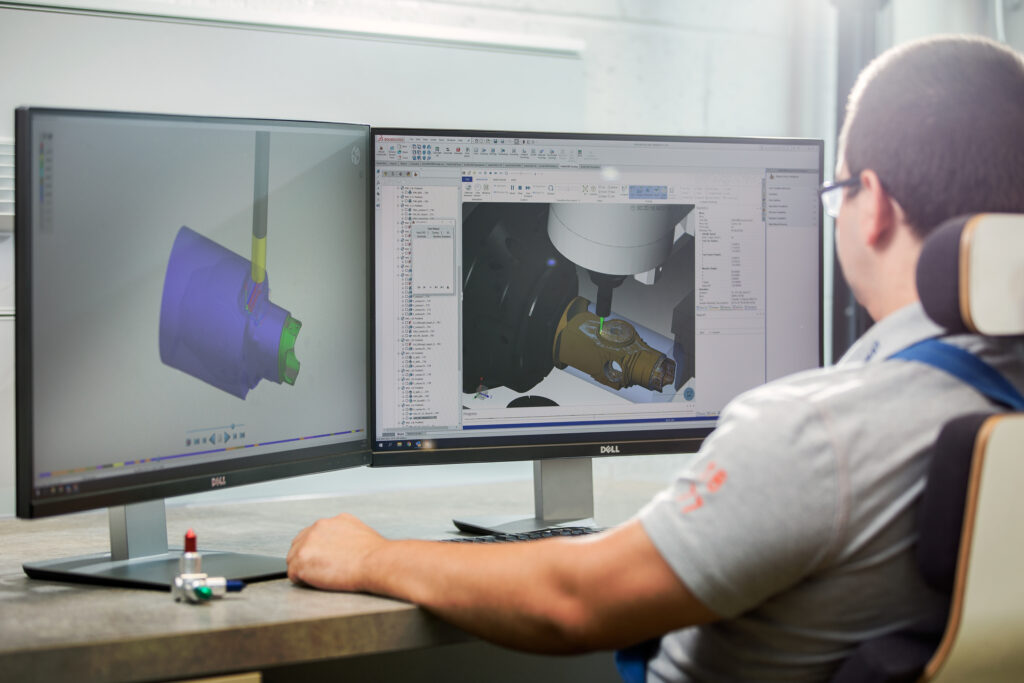
1. Programming
A program based on the customers drawing is created using SolidCAM.
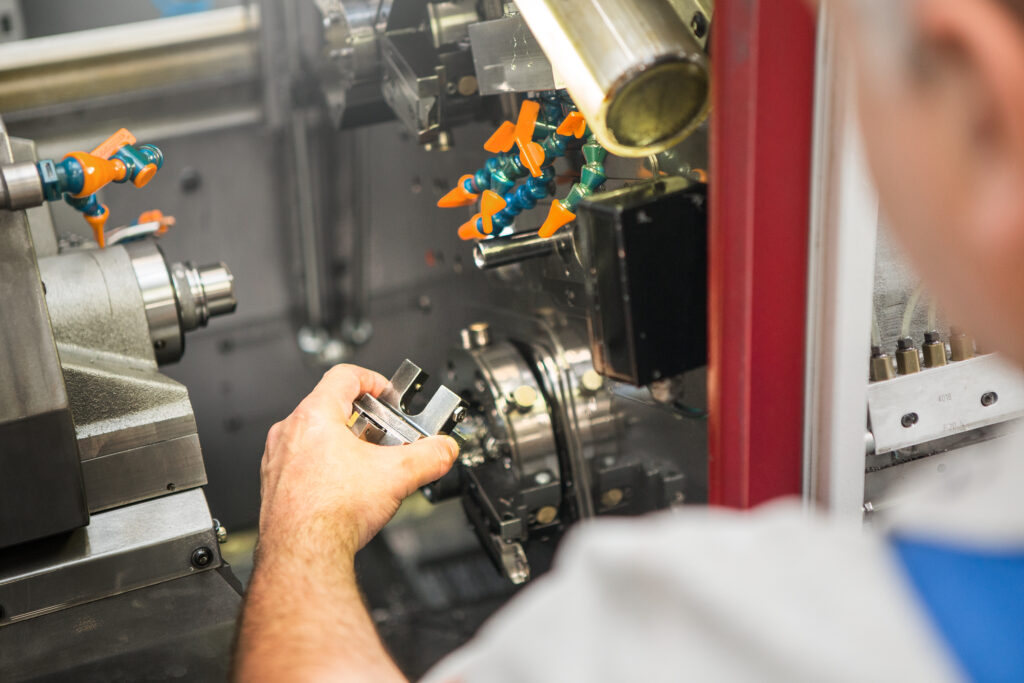
2. Setup
We load the program into the workbench, calibrate and attach appropriate tools and fill the bar loader.
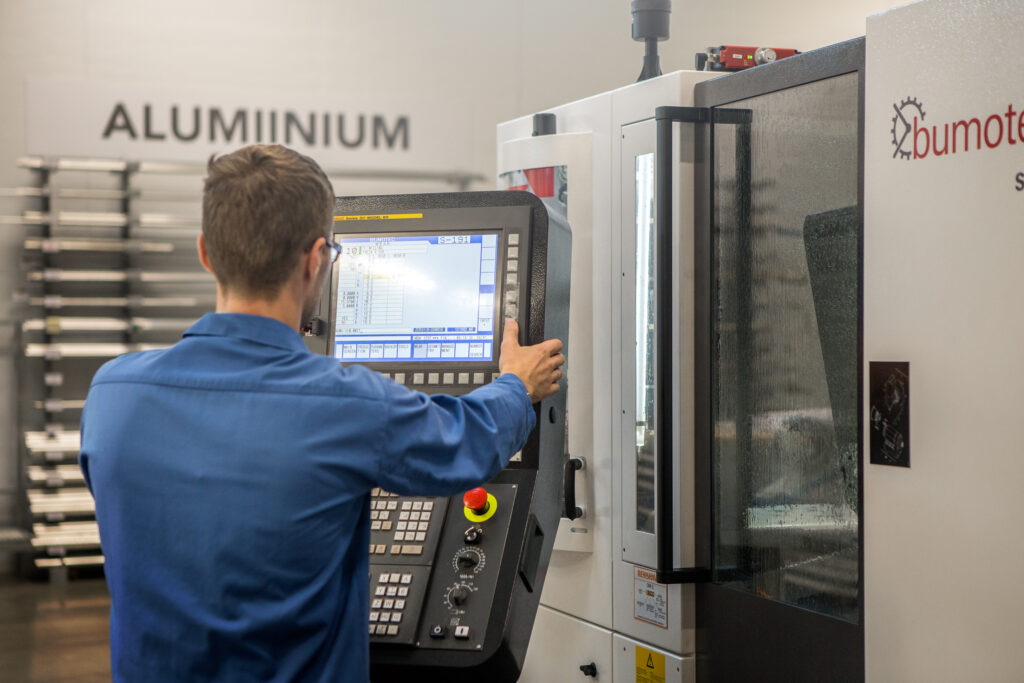
3. Manufacturing
Besides monitoring the machine, the operator is tasked with taking part measurements at fixed intervals.
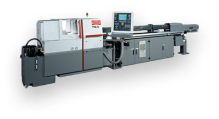
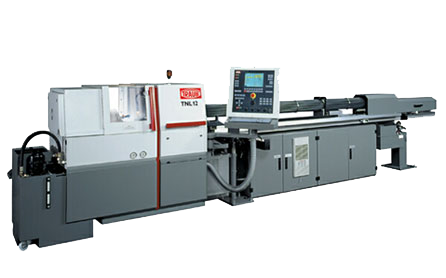
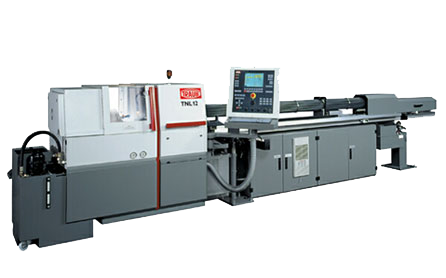
TRAUB TNL - 12
Year 2008, year 2012Highly precise long turning technology with a diameter of up to 16 mm, with a maximum of four tool carriers and innovative control concept.
High production rates due to simultaneous machining with up to four tool carriers at two identical spindles; 0.3 sec chip-to-chip time
Two tool carriers with X- and Z-axis and six stations each for driven tools
Front and rear working each have one tool carrier, which have four stations per carrier
Minimal tool interference because of the patented arrangement of four tool carriers in two intersecting planes
Universal tooling, short setup times using the comprehensive tooling system, the patented tool mounting and preset tool holders
Good accessability in spite of the compact architecture; exterior dimensions are independent of equipment options
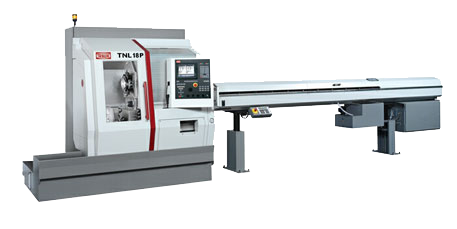
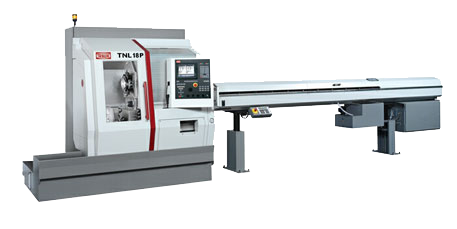
TRAUB TNL - 18P 7B
Year 2012Sliding headstock automatic lathe with a diameter of up to 20 mm for turning with and without a guide bush.
Simultaneous machining with up to 3 tools possible
Easy change-over for turning operation with and without a guide bush
Clearly structured working area with large axis travels
Turret indexing using an NC rotary axis
Very large pool of fixed and driven tools by using double and triple holders 3-axis grasping with counter spindle
Excellent accessibility for operation and maintenance due to large sliding door
Compact design at minimum footprint
New TX8i-p production control
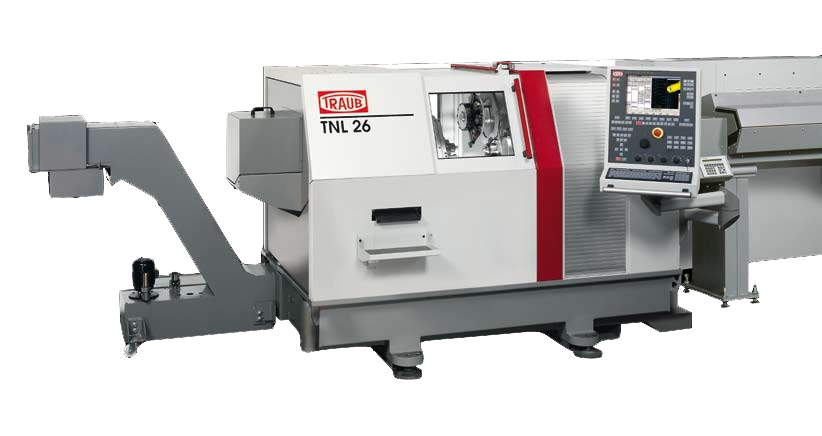
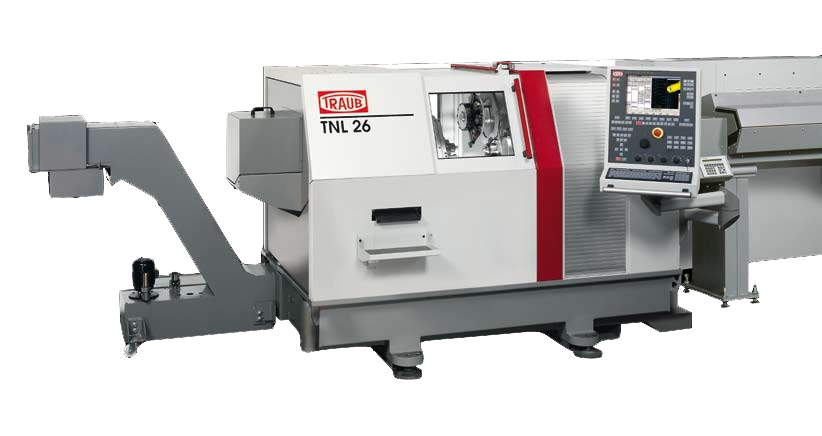
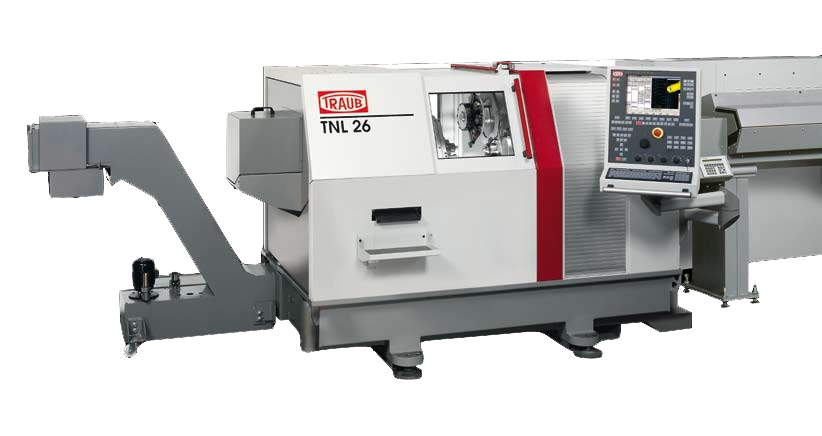
Traub TNL - 26
Year 2005Sliding headstock automatic lathe with a diameter of up to 20 mm for turning with and without a guide bush.
High production rates due to simultaneous machining with up to 4 tool carriers at the main and counter spindle; chip to chip time 0.55 sec.
Main and counter spindle with hollow shaft motors and synchronous drive technology 2 tool carriers, used as multifunctional turrets with high speed indexing and 12 stations (individually or centrally driven)
Front attachment with 5 or 7 stations for fixed and driven tools
Backworking with tool drive for up to 5 tools
Minimal tool interference due to patented arrangement of all tool carriers in two intersecting working planes
Standard tooling and fast tool mounting as well as short setup times
Easily accessable work area from both sides
Compact footprint
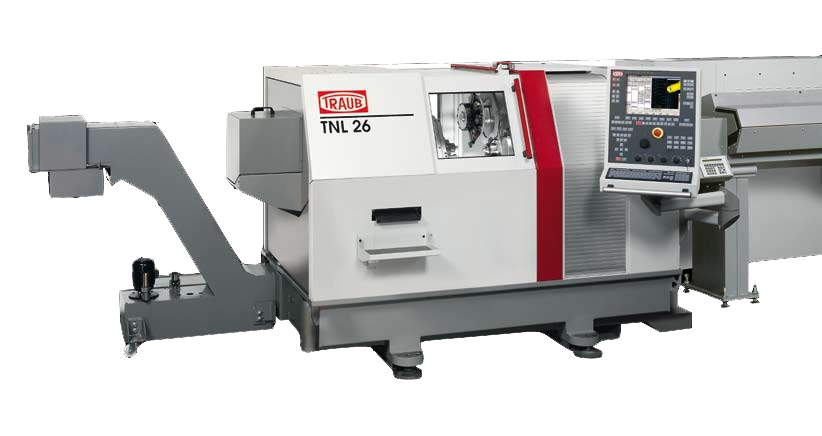
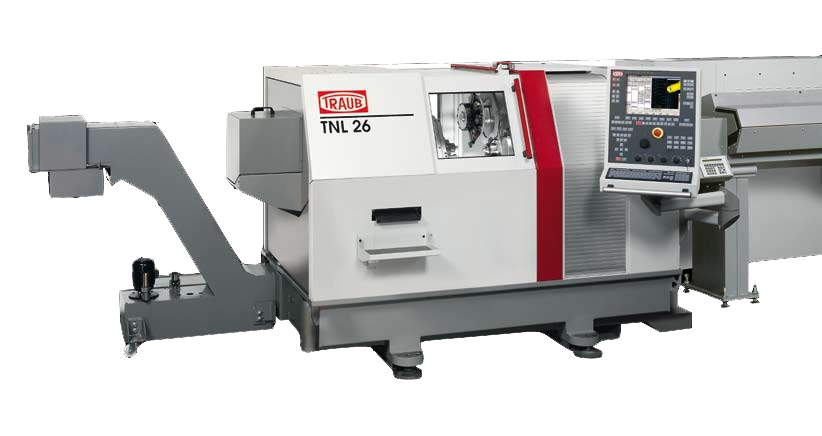
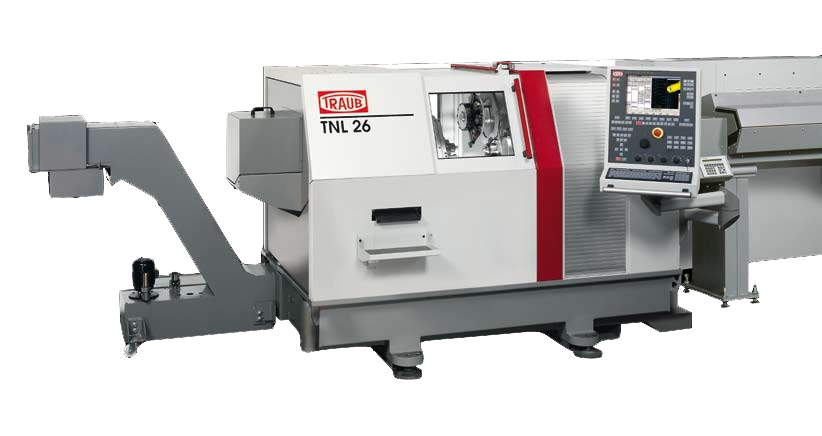
Traub TNL - 26 K
Year 2010CNC long turning machine with a maximum spindle opening of 32 mm. The machine has a modular design and up to four tools can be used simultaneously depending on the configuration level.
High production rates due to simultaneous machining with up to 4 tool carriers at the main and counter spindle; chip to chip time 0.55 sec.
Main and counter spindle with hollow shaft motors and synchronous drive technology 2 tool carriers, used as multifunctional turrets with high speed indexing and 12 stations (individually or centrally driven)
Front attachment with 5 or 7 stations for fixed and driven tools
Backworking with tool drive for up to 5 tools
Minimal tool interference due to patented arrangement of all tool carriers in two intersecting working planes
Standard tooling and fast tool mounting as well as short setup times
Easily accessable work area from both sides
Compact footprint
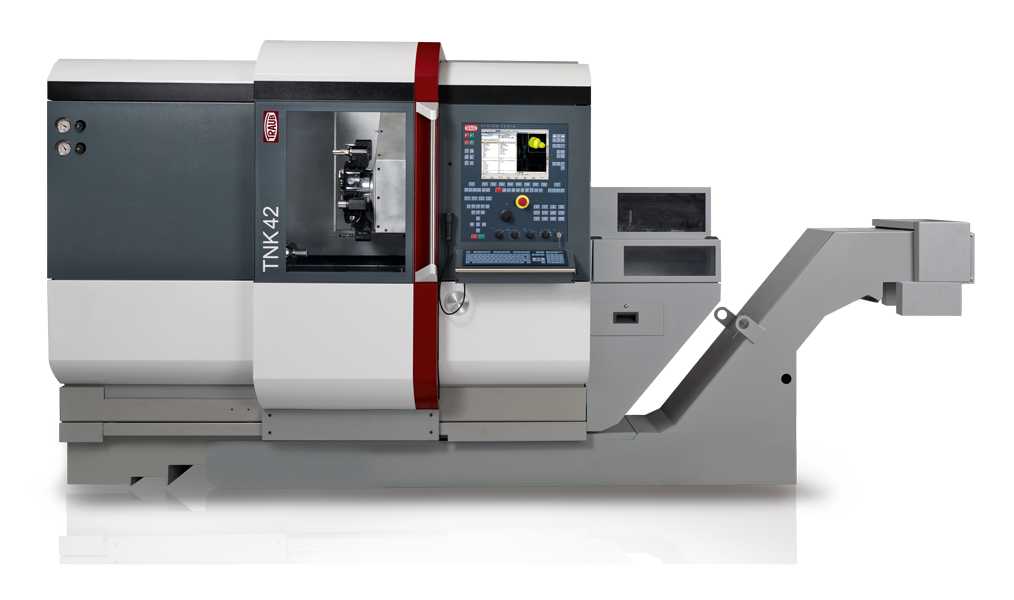
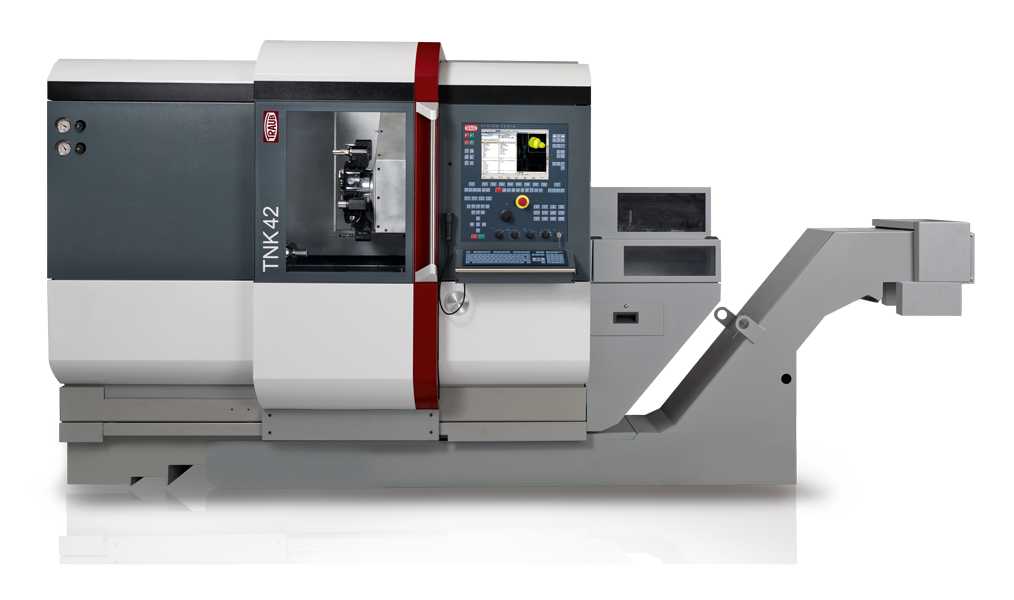
Traub TNK - 42
Year 2013Fixed headstock turning machine with a 42 mm spindle clearance and a 305 mm turning length.
2 work spindles, 2 turrets and 1 back working attachment
Compact machine design with up to 3 simultaneously working tool carriers allows high productivity
Only 5.5 sqm floor space
Turret indexing as NC rotary axis and Dual Drive system allow chip-to-chip times of 0.4 seconds
Dual function of the lower X/Z slide:
Tool turret and swiveling counter spindle for rear end machining
8 tool stations for extensive rear end machining
Workpieces are removed fast and gently by a CNC-controlled shuttle
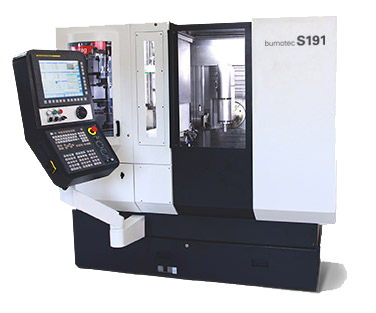
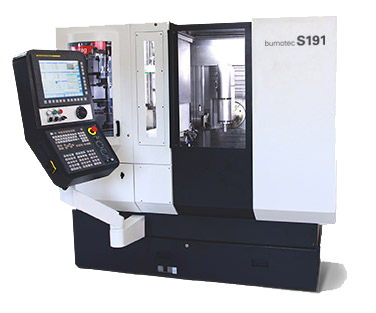
Bumotec s191H-FTL-RP
Year 2018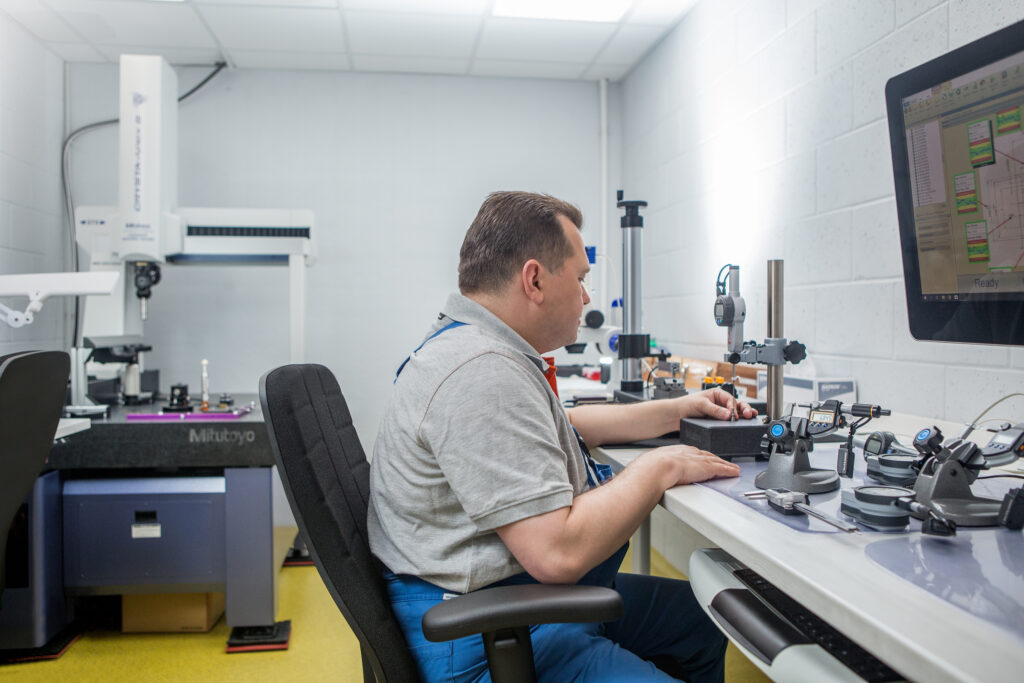
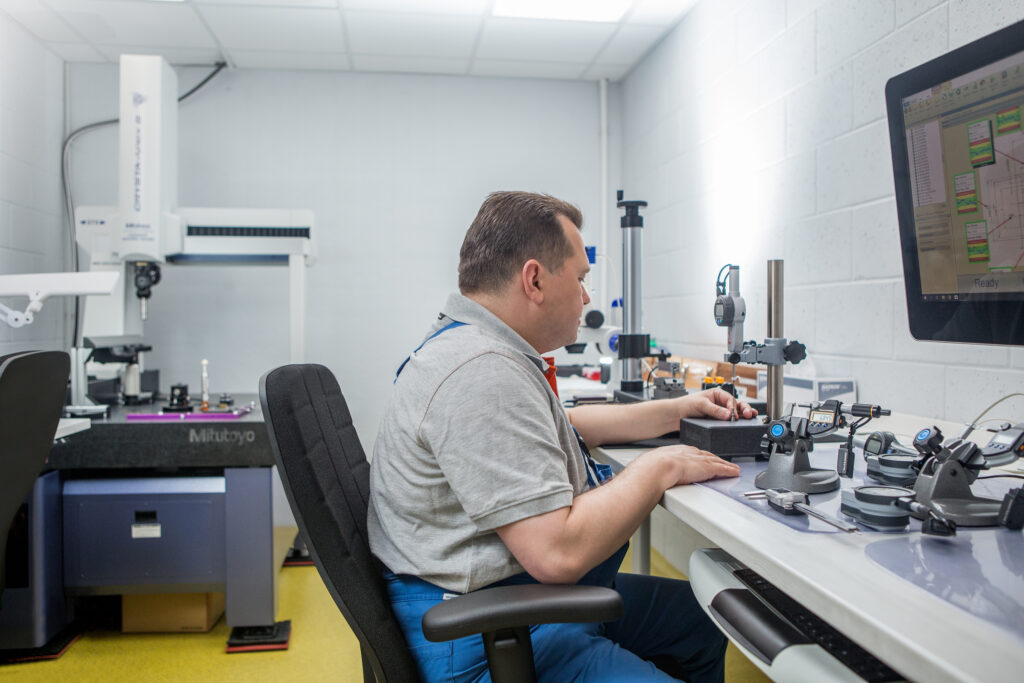
4. Quality Control
Our company has developed a unique three-stage system of quality control that allows us to guarantee 100% quality of the produced parts. We operate state of the art Mitutoyo measuring tools and analyse the data with MeasurLink. We also offer this measurement capability as a service.
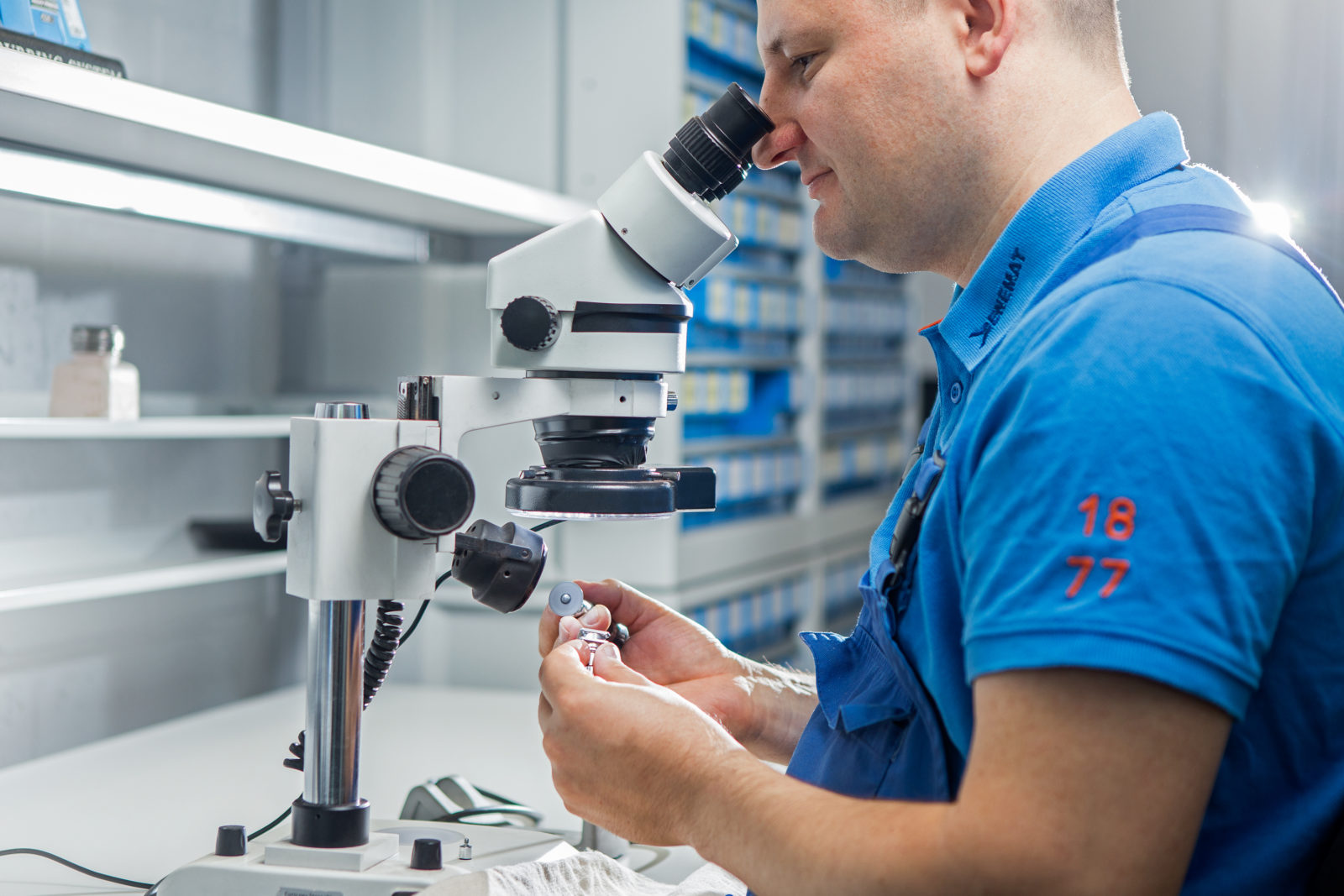
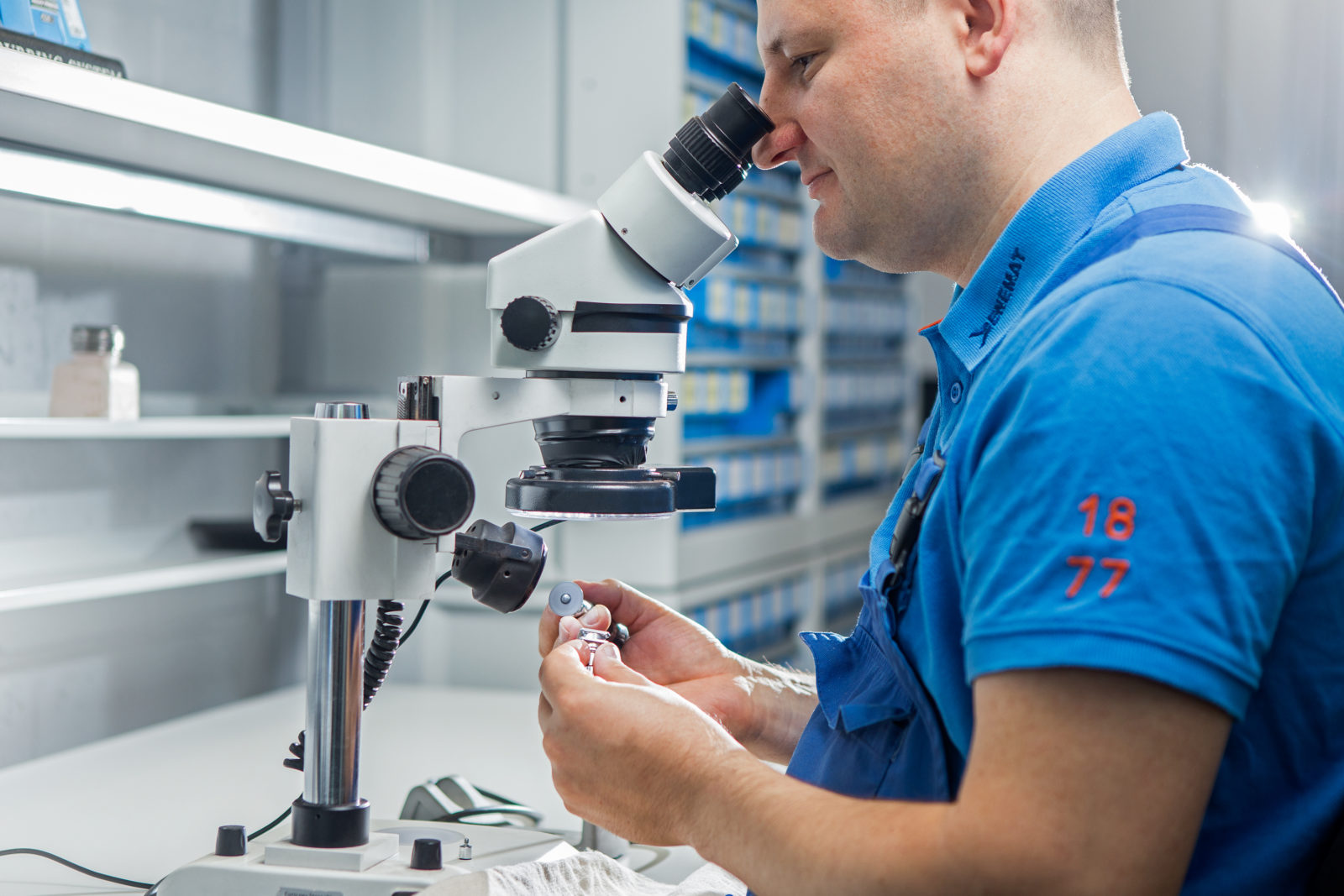
5. Finishing
Burr, even in the least accessible places, is successfully removed under the microscope. Additionally wet & dry centrifugal deburring and magnetic polishing machines can be utilized.
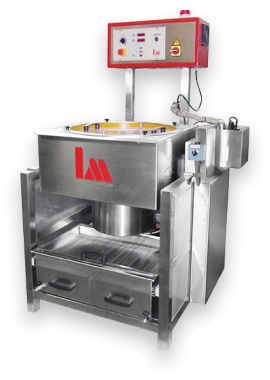
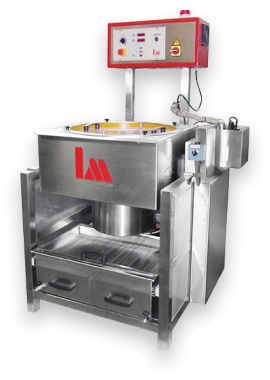
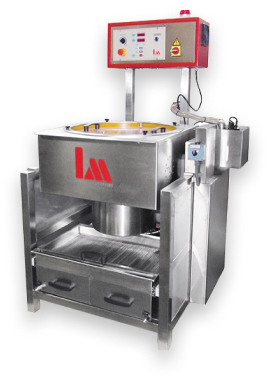
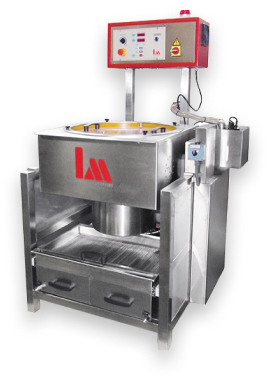
LM Magnetic Polishing Machine Mod. 3000
Year 2013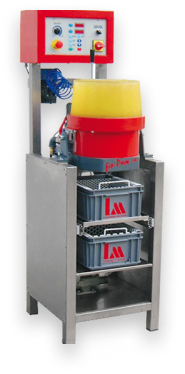
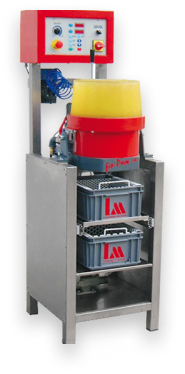
Lm Turbo Eco Drive 15 Lt.
Year 2013Wet and dry centrifugal deburring and polishing machines.
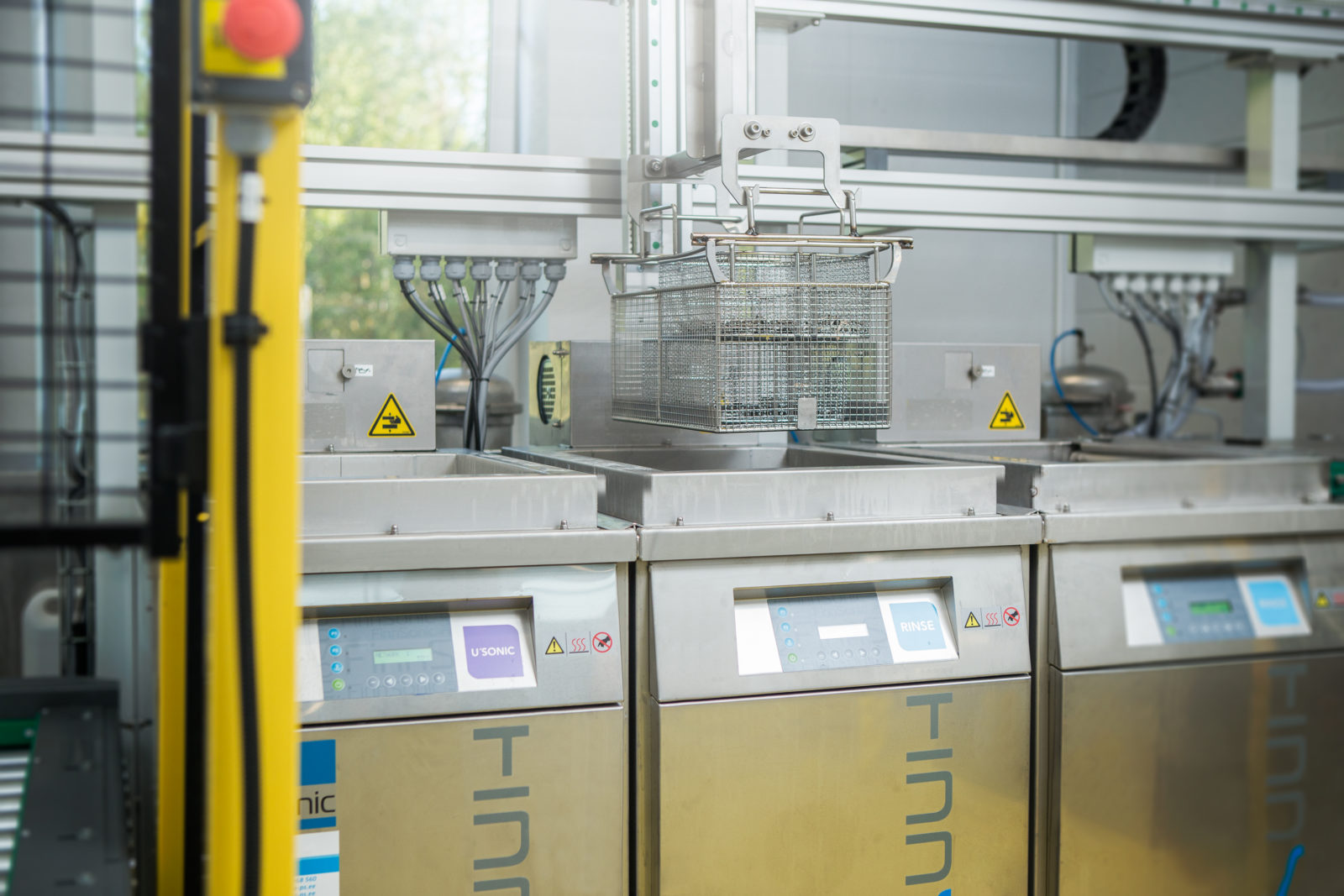
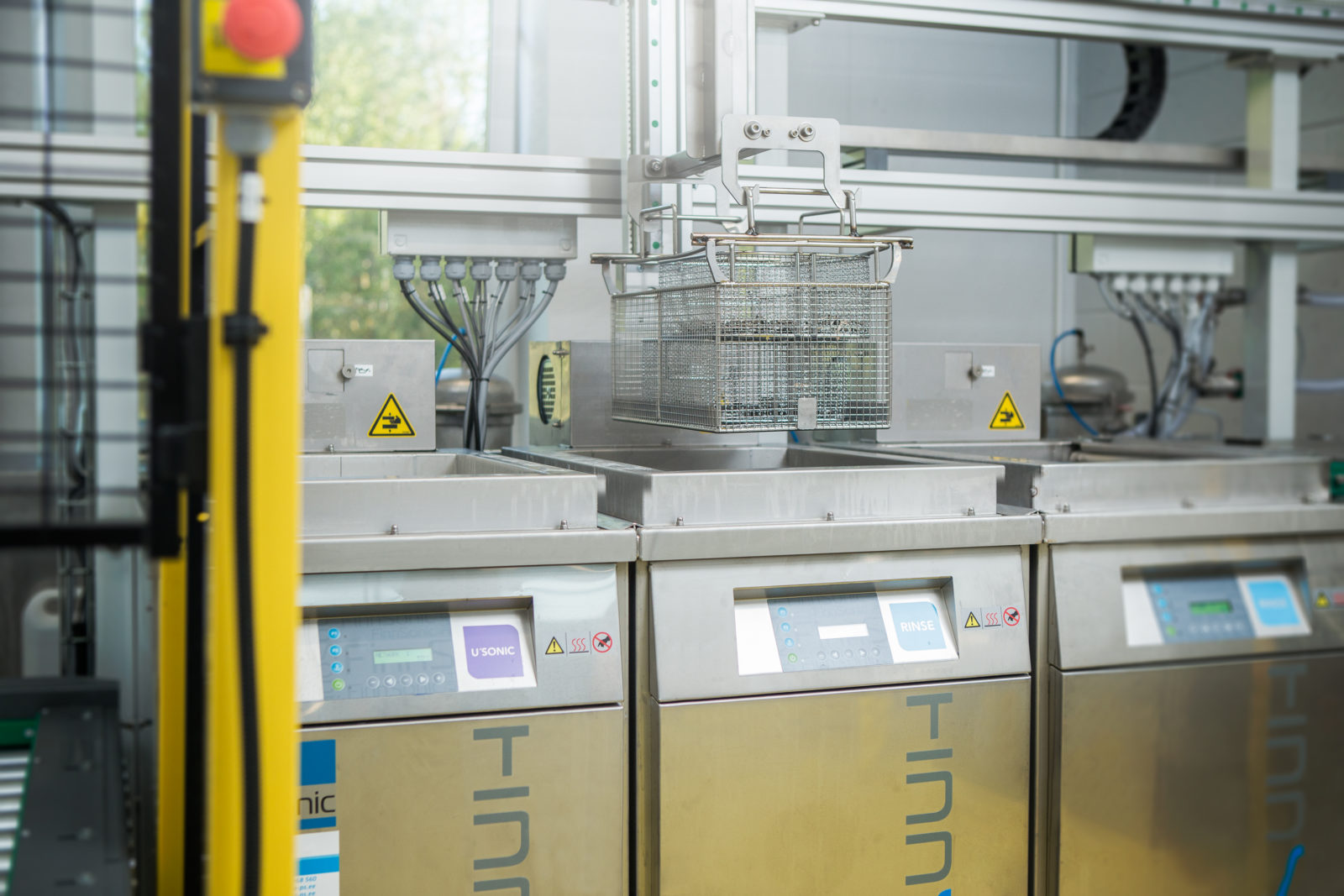
6. Cleaning
Finally the parts undergo washing, drying and are packaged as requested.
FinnSonic Versa Genius
In 2019 we invested in a fully automatic multi-stage cleaning line which can accommodate the various requirements of parts and helps use reduce or environmental footprint.